The application of copper foil in lead frames is mainly reflected in the following aspects:
●Material selection:
Lead frames are usually made of copper alloys or copper materials because copper has high electrical conductivity and high thermal conductivity, which can ensure efficient signal transmission and good thermal management.
●Manufacturing process:
Etching: When making lead frames, an etching process is used. First, a layer of photoresist is coated on the metal plate, and then it is exposed to the etchant to remove the area not covered by the photoresist to form a fine lead frame pattern.
Stamping: A progressive die is installed on a high-speed press to form a lead frame through a stamping process.
●Performance requirements:
Lead frames must have high electrical conductivity, high thermal conductivity, sufficient strength and toughness, good formability, excellent welding performance and corrosion resistance.
Copper alloys can meet these performance requirements. Their strength, hardness and toughness can be adjusted through alloying. At the same time, they are easy to make complex and precise lead frame structures through precision stamping, electroplating, etching and other processes.
●Environmental adaptability:
With the requirements of environmental regulations, copper alloys meet the green manufacturing trends such as lead-free and halogen-free, and are easy to achieve environmentally friendly production.
In summary, the application of copper foil in lead frames is mainly reflected in the selection of core materials and the strict requirements for performance in the manufacturing process, while taking into account environmental protection and sustainability.
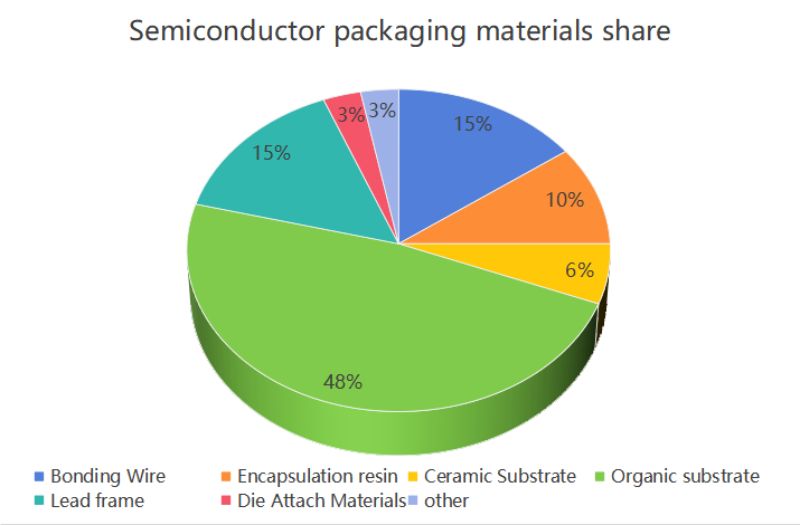
Commonly used copper foil grades and their properties:
Alloy Grade | Chemical composition % | Available thickness mm | ||||
---|---|---|---|---|---|---|
GB | ASTM | JIS | Cu | Fe | P | |
TFe0.1 | C19210 | C1921 | rest | 0.05-0.15 | 0.025-0.04 | 0.1-4.0 |
Density g/cm³ |
Modulus of elasticity Gpa |
Thermal expansion coefficient *10-6/℃ |
Electrical conductivity %IACS |
Thermal conductivity W/(m.K) | |||||
---|---|---|---|---|---|---|---|---|---|
8.94 | 125 | 16.9 | 85 | 350 |
Mechanical properties | Bend properties | |||||||
---|---|---|---|---|---|---|---|---|
Temper | Hardness HV |
Electrical conductivity %IACS |
Tension test | 90°R/T(T<0.8mm) | 180°R/T(T<0.8mm) | |||
Tensile strength Mpa |
Elongation % |
Good way | Bad way | Good way | Bad way | |||
O60 | ≤100 | ≥85 | 260-330 | ≥30 | 0.0 | 0.0 | 0.0 | 0.0 |
H01 | 90-115 | ≥85 | 300-360 | ≥20 | 0.0 | 0.0 | 1.5 | 1.5 |
H02 | 100-125 | ≥85 | 320-410 | ≥6 | 1.0 | 1.0 | 1.5 | 2.0 |
H03 | 110-130 | ≥85 | 360-440 | ≥5 | 1.5 | 1.5 | 2.0 | 2.0 |
H04 | 115-135 | ≥85 | 390-470 | ≥4 | 2.0 | 2.0 | 2.0 | 2.0 |
H06 | ≥130 | ≥85 | ≥430 | ≥2 | 2.5 | 2.5 | 2.5 | 3.0 |
H06S | ≥125 | ≥90 | ≥420 | ≥3 | 2.5 | 2.5 | 2.5 | 3.0 |
H08 | 130-155 | ≥85 | 440-510 | ≥1 | 3.0 | 4.0 | 3.0 | 4.0 |
H10 | ≥135 | ≥85 | ≥450 | ≥1 | —— | —— | —— | —— |
Post time: Sep-21-2024